LISTENING
STUDY Question 44:
What is the availability of tree-free pulping facilities,
and future outlook?
Figure
1. 1998 Non Wood Pulping Capacity
(click for larger picture)
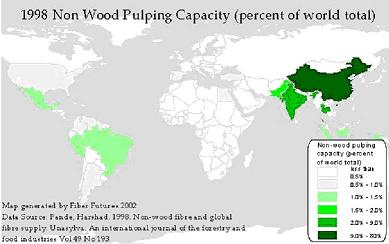
Current
Status, U.S. and International
Ag
pulping facilities are very limited at the moment. I
am aware of very few such facilities (2-3) in the US
that can presently pulp ag fibers. - Jeff Lindenthal,
President, Green Field Paper Company
There are several mills in North America with
the ability to process and make paper out of certain
tree-free fibers, mostly recovered cotton fibers. And
some of these mills can and do make papers using other
tree-free fibers.
But the vast majority
of papermaking facilities are geared toward making paper
from trees. For example, with alternative fibers, it
can be more difficult to remove the water during papermaking,
and that can create a large cost disadvantage. Tree-based
paper machines would not be able to efficiently drain
water out of tree free fibers at their current configuration,
which is designed to make paper profitably.
The paper machines
that are currently making cotton, kenaf, or hemp are
generally set up differently to be able to make paper
profitably from these different fibers, but the cost
structure is higher. I'm sure tree-based paper manufacturers
could use cotton/hemp/kenaf on their big machines, slow
the machines, increase suction, and increase drying
temperatues and make the hundreds of other alterations
that need to be made. However, there's no financial
incentive for them to do that until people say they
only want papers that include alternative fibers. They,
like everybody else, have to make a profit. -
Peter Hopkins, Environmental Papers Consultant for
Crane Paper Company, Gargan Communications
There are three to four mills that can pulp nonwood
fibers (Kimberly Clark, Ecusta, and Dexter). Dexter
pulps nonwoods for high quality, highly specialized
medical and technical grade papers. There were a number
of small Chinese straw pulping mills, but the government
is shutting them down due to their high effluent output.
Mexico has a bagasse pulping mill. - Tom Rymsza,
President, Vision Paper
Currently agricultural fiber pulping facilities
are very limited and generally dedicated to producing
technical pulps for specific applications. - Living
Tree Paper Company
Figure
2. 1998 Estimated Non Wood Pulping
Capacity
(click for larger picture)
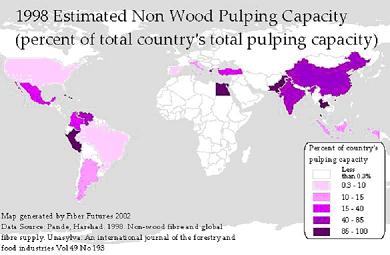
In
Australia, Arisa is raising funds to build a 38,000
ton/yr bleached wheat straw market pulp mill at Horsham,
Vic. Pulping is to be by the Naco Process, with start-up
aiming for 2001. Silica content removal (desilication)
will take place at 3 stages - namely, on the straw (NaOH
treatment); in the green liquor (lime addition); and
in the effluent treatment plant. - Higgins
2000
China pulps both wheat and rice straw, and accounts
for 75% of total world straw production. The large pulp
mills utilizing wheat straw are mainly located in Europe.
The Danish Fredericia mill, which was the only dedicated
wheat straw market pulp mill in Europe (the other mills
being integrated with paper production) and the Spanish
Saica pulp mill are both thought to have been shut down.
The new Cellpaille
mill, in France, is using a Saica digester and soda
cook, with spent liquor recovery/treatment by the LPS
Process (Granit). The spent black liquor is acidified
to pH 2.5-3 to precipitate the lignin, which is then
processed, washed, dried and sold for uses similar to
those for lignosulfonates (although it is sulfur-free).
The resulting filtrate is treated by wet air oxidation
(SRS Process; sodium recovery system), with oxygen being
utilized rather than air. - Paperloop.com,
"Wheat Straw and Rice Straw"
There
are essentially no pulping facilities for agricultural
fibers in the U.S. or Canada. Exceptions are two facilities
for pulping high value, specialty fibers and the very
small straw pulping unit of Arbokem. There is a mill
in Mexico that pulps bagasse, the residual cane after
sugar extraction. This pulp is used in various paper
grades. Worldwide, 7-8% of the total virgin pulp fiber
production is from nonwood materials. - Michael
Jackson, Consultant, Tolovana Park, OR
14
flax pulp mills, production capacity about 75,000 tpa
23 hemp pulp mills, production capacity about 80,000
tpa
9 abaca pulp mills, production capacity about 35,000
tpa
U.S. - 2 mills w/ max 20,000 tpa hemp pulp production
Phillipines - 1 mill w/ max 8,000 tpa abaca pulp production
- Judt 1993
Figure
3. World Papermaking Pulp Capacity
(click for larger picture)
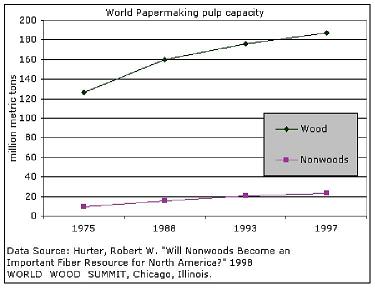
In the U.S., paper was traditionally made from
non-woods, mainly waste products from the textile industry.
During World War II, there were 25 mills in the midwest
producing corrugating medium from wheat straw. The last
straw pulp mill closed by the end of 1960. Non-wood
fibers were no longer competitive for four reasons:
- Development of the kraft recovery system as an efficient
means for recovering spent chemicals in wood pulping;
- Increases in labor cost in a labor-intensive industry:
straw harvesting, storage and pulping technologies
were less economic than similar wood-based processes;
- Westward shift of the agricultural production:
straw as a fiber source moved further away from the
pulp and paper industry and its customers; and
- Increases in fuel cost: paper mills' access to
bagasse, a waste product from sugar refining, declined
as sugar mills switched back to using it as a fuel
source when prices for other fuels increased.
- Environmental Defense Fund Paper Task Force,
White Paper 13, "Non-Wood Fiber Sources"
Future Outlook
Pandia
digester, a continuous digester specially designed for
nonwood pulping, is available. But a wood digester can
be also used in nonwood pulping. As far as future outlook,
especially in the U.S., the price of wood chips is falling
and the U.S. trade deficit in paper and board has widened
significantly since 1996. For the first time in many
decades, U.S. paper and paperboard production capacity
has actually declined. American farms are already subsidized
and two major crops - corn and wheat residues - could
be converted into pulps. Several dozen small digesters
can be installed in corn and wheat belts and start producing
pulps. Future outlook seems to me is based more on the
control of imports and national policy rather than availability
of agricultural pulping facilities. Without a national
policy, cheap imported chips, pulps, and papers will
flood the U.S. market. - James S. Han, Research
Chemist, USDA Forest Service Forest Products Laboratory
There is the potential for large-scale commercialization
of tree-free paper, but there remain a number of obstacles,
many of them agricultural. As Daniel Kugler's report
"Non-Wood Fiber Crops" demonstrates, a major barrier
is the lack of processing plants and commercial-scale
agricultural equipment. Many of the test plots have
been harvested using equipment borrowed from other industries,
including sugar cane and cotton. But kenaf harvesters
have been built and tested. These problems would be
easily overcome if the industry were focused on them.
- Jim Motovalli, "The Paper Chase"
There
are a couple of projects underway, though we cannot
expect to see results for 2-5 years. - Jeff
Mendelsohn, President, New Leaf Paper
Two
of the characteristics of nonwood fiber use about which
there appears to be relatively widespread general agreement
are the seasonality of annual crops and the transport
costs of moving low bulk density agricultural fibers.
From the established paper industry's point of view,
both compare unfavorably to wood, which can be harvested
year-round and stored indefinitely, and is much denser
than agricultural fibers and thus comparatively less
expensive to transport. Agricultural pulp mills continue
to be contemplated (though not built) at scales of up
to 500-600 tpd. However, there is increasing agreement
that for reasons of transport efficiency and fiber supply
security, the optimal scales for agricultural pulp production,
even in developed countries, should be much smaller.
. . . Generally, the transport issues associated with
nonwoods, the corollary emphasis on smaller-scale pulping
formats, and the issues of heterogeneity in fiber types,
sources, and applications, are the basis of an increasingly
strong regional theme that runs through the debate.
- Maureen Smith, The U.S. Paper Industry and Sustainable
Production
There
are limited nonwood pulping facilities. Cotton pulp
mills are probably the most readily available. Vision
Paper is working on developing a dedicated pulp mill
focusing on kenaf.
A new nonwood mill
will give kenaf viability in the mainstream paper market.
Many pulp mills that are in use were built over fifty
years ago. It has been over a decade since a new pulp
mill has been constructed. There have been improvements
in the efficiencies and environmental systems for pulp
mills in recent years. Vision Paper's mill will take
advantage of these advancements. Working with a raw
material which pulps with less chemicals and energy
than trees gives kenaf another economic advantage. We
expect that the mill will be producing tree-free pulp
that will cost less than tree-pulp, furthering market
advancement.
The mill is designed
to use local agricultural resources. The design can
be easily replicated so subsequent mills can be constructed
as demand increases. - Tom Rymsza, President,
Vision Paper
Led
by entrepreneurs such as Nile Fiber, Mells Industries,
etc. on the forefront, and traditional leaders such
as Buckeye Technologies, the future of nonwoods is exciting
in all of the fields (annuals, herbaceous, residues,
processing waste). We will continue to see more natural
product such as feminine hygiene, cigarette papers,
etc., where consumers prefer cotton and other natural
fibers over the synthetics. For example, we will have
kenaf placemats with an antimicrobial agent to ensure
a clean eating area. The markets are limitless.
- Peter A. Nelson, President, AgroTech Communications,
Inc.
All
Kraft and TCF mills can run Arundo donax. We are negotiating
new licensees as we speak. Also, Samoa-Pacific has the
ability to sub-license. - Ernett Altherimer,
Founder and Chairman, Nile Fiber
It
doesn't seem like there are many, though I'm not an
expert. Arbokem was built to focus on agricultural fiber
use. All the others sound like they're on the West Coast.
As far as the market expanding in the next years, there
are a number of hurdles such as raw materials only being
available once a year rather than year round. Trees
can store for extended periods of time whereas rot and
decomposition threaten bales of straw.
The industry needs
to do a better job at putting their nonwood materials
side by side with trees to understand as a country which
papers are preferable. There is a lot of support on
"the hill" for agriculture based products. On the other
hand, the forestry industry has a lot of lobbyists.
Without good information, the industry is not going
to get far. - Russell Clark, Environmentally
Preferable Purchasing Program, US EPA
Economics are the biggest barrier for nonwoods
going into the niche markets. They may not have an advantage
because people may not see trees as toxic. Whereas consumers
might believe that agricultural products were grown
with pesticides, they could believe trees just grew
in a forest and must be natural. - Russell
Clark, Environmentally Preferable Purchasing Program,
US EPA
The
issue of agri-pulping in developed countries is complex.
Some of these barriers are very difficult to overcome.
One of the most important pathways to "save trees" is
to use less paper, but this approach is contrary to
the growth-oriented market economy.
See for example,
my presentations, "Agricultural Fibers for Pulp and
Paper Manufacture in Developed Countries," "How Many
Trees Can Be Saved?," "Experience in the Technical and
Market Development of Agri-Pulp Printing Papers in North
America," and "Obstacles and Opportunities in the Development
of an Agri-Pulp Industry in the Pacific Northwest."
- Al Wong, Founder, Arbokem
While
some experimentation has been done with agricultural
residuals in papermaking, there is a very small opportunity
to use residual fibers based on the fact that papermaking
facilities are often far from sources of agricultural
residuals. Shipping, handling, and storing costs would
be high relative to those for wood. Building facilities
dedicated to pulping agricultural materials would seem
to be a very high risk venture. - International
Paper
Various
companies are working on a desilication process. So
far, the best process has been developed by the Central
Pulp and Research Institute (CPPRI) for a newsprint
mill in India, with assistance from the United Nations
Industrial Development Organization (UNIDO). The process
should eliminate 70-80% of the silica, but requires
further testing in commercial operations. - Environmental
Defense Fund Paper Task Force, White Paper 13, "Non-Wood
Fiber Sources"
My
goal is to build a series of dedicated kenaf pulp mills
that would be the cleanest pulp mills in the country
(world), utilizing bioenergy, and producing cost-competitive
products. - Tom Rymsza, President, Vision Paper
The
Malaysian research and development center, Technology
Park Malaysia (TPM) . . . is conducting research on
manufacturing paper from banana stems. . . . [I]t plans
to work with companies in Australia and Japan that are
already in the early stages of banana paper production.
TPM laboratory technician and researcher Nurul Huda
Muhammad estimates that around 1 billion tonnes/yr of
banana stems are left to rot. Japan's Banana Paper Project
Supporting Association (BPPSA) is still in talks with
the country's Ministry of Foreign Affairs and the United
Nations on plans to establish banana paper mills in
100 developing countries. . . . The BPPSA has already
set up facilities in Haiti and Jamaica and hopes to
build the others by 2015. - Paperloop.com,
"Malaysia studies banana paper production," July 2,
2004
Click Here for Table 6:
Leading Users of Nonwood Fibers in Papermaking
Transform
Australia is rebuilding its PM to raise output of banana
tree fiber-based paper to 20,000 tonnes/yr. The unit
produced just 2,000 tonnes last year. The plant, which
is located in North Queensland, the banana-growing region
of Australia, is touted as the world's only manufacturer
of 100% banana paper. . . . "There's just one hurdle
to go through," Johnston told Paperloop. The director
explained that the firm needs more investors. Transform
Australia claims banana paper is 300 times stronger
than pulped paper, is water resistant and greaseproof,
but fully biodegradable and environmentally friendly
in that it is made using what is currently a waste product.
The firm indicated that no additives, chemicals, glues
or dyes are used in production. Water is not used either
as the trees contain enough of their own sap to re-bond.
The company believes banana paper can replace 85% of
current world consumption. - Paperloop.com,
"Transform Australia to Boost Banana Paper Output,"
June 18, 2004
How
does a paper qualify for environmentally sound manufacturing
practice?
- When
it does not deplete the forest cover,
- when
it makes use of waste agricultural residues like cereal
straws, which otherwise pose a problem in proper disposal,
- when
there are no effluents from the process which are
toxic to the environment - land, water and air natural
resources,
- when
it offers sustainable practice by not depleting a
limited quantity of natural resource,
- when
it is less dependent on external energy inputs by
using internal process energies like cogeneration
of steam and electricity,
-
when it allows blending with wood fibres to make better
quality paper at lower cost and lesser negative impact
on the environment.
Taking
cognisance of all available state of the art pulp and
paper making technologies available in the world today,
we have the solution which satisfies all above criteria
and in addition it is also economical and cost efficient.
We know how to make
paper from cereal straws. This is a plentiful agricultural
waste in India and we thought why not put this to good
use. In India many small plants were set up. One of
them was ours - Amrit Papers. The pollution control
Board of the Punjab state government told us that we
couldn't enhance capacity unless we cleared up the mess
we were creating with the black liquor effluent. We
searched worldwide and took a lot of efforts (for a
small enterprise). So we finally achieved success with
the homegrown MKCR (Mahesh Khaitan Chemical Recovery
technology, named after the inventor) and were given
a patent too.
We made bench and
lab models and finally a pilot facility was run for
5 years until we had tweaked the process to perfection.
We want to set up
the first facility of 150 Tonnes per day pulping capacity
based mostly on cereal straws, somewhere near Delhi
or in Punjab. . . . We want to team up with a financial
investor. - R. Santhanam, Vice President, Amrit
Environmental Technologies
|